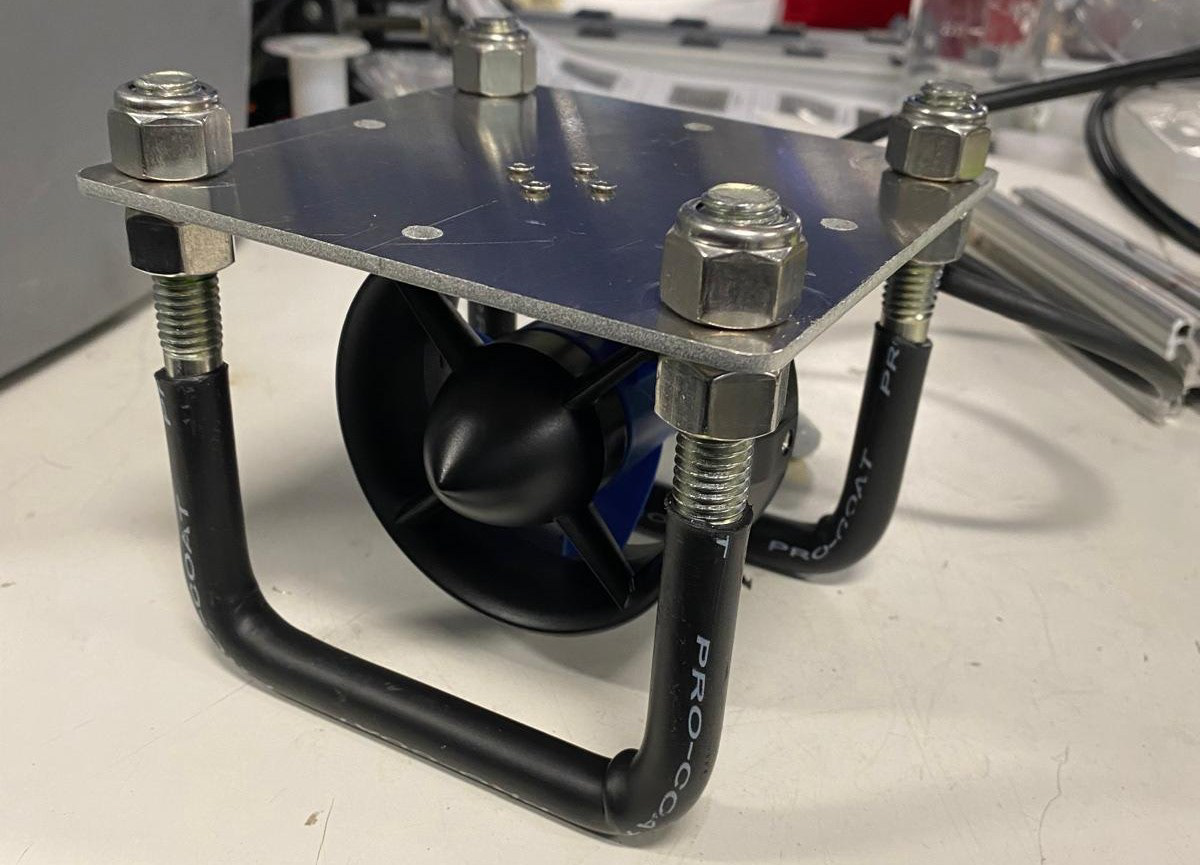
Skills
CAD
CNC Machining
Collaborators
Sam Huang
Tony Tang
Project Overview
As part of our work on the Arcturus Flagship for the RoboBoat competition, I led the development of a versatile thruster mounting system. The project required careful consideration of both structural integrity and adaptability to meet the demanding requirements of an advanced propulsion system. Utilizing cutting-edge CAD tools and precision fabrication techniques, we produced a robust solution that contributed significantly to the boat’s overall performance.
Problem Definition
The new MIT Arcturus flagship required a protective shield for its thrusters, which needed to be lightweight yet strong enough to support the entire weight of the boat when placed on the ground. The challenge was to design a structure that would not compromise the boat's performance while providing the necessary protection and load-bearing capability.
Design Process
Our project began by evaluating thruster shield designs from previous RoboBoat competition teams, which provided a foundation for our approach. I led the design of the thruster mounting system using Fusion360, focusing on creating a versatile and durable mounting plate that would securely connect the thruster and shield to the hull of the boat. The mounting plate featured a circular array of strategically placed mounting points, allowing for the thruster to be adjusted to various angles to meet the needs of the X-Drive configuration. This adjustability was crucial for optimizing the boat’s maneuverability.
To ensure both durability and corrosion resistance, I selected a quarter-inch marine-grade aluminum sheet for the thruster mounting plate. The material’s strength and resistance to harsh marine environments made it ideal for this application. The plate was designed with precise hardpoints for securing the thruster using T-nuts and screws, ensuring a stable and reliable connection.
For the support system, I chose square, rubber-cushioned U-shaped bolts made from zinc-plated steel. These bolts were specifically selected for their ability to bear the entire load of the boat on a single thruster, providing both stability and shock absorption. The completed design was then integrated into the overall ship CAD model using Onshape, enabling seamless collaboration with the team and allowing for iterative refinements.
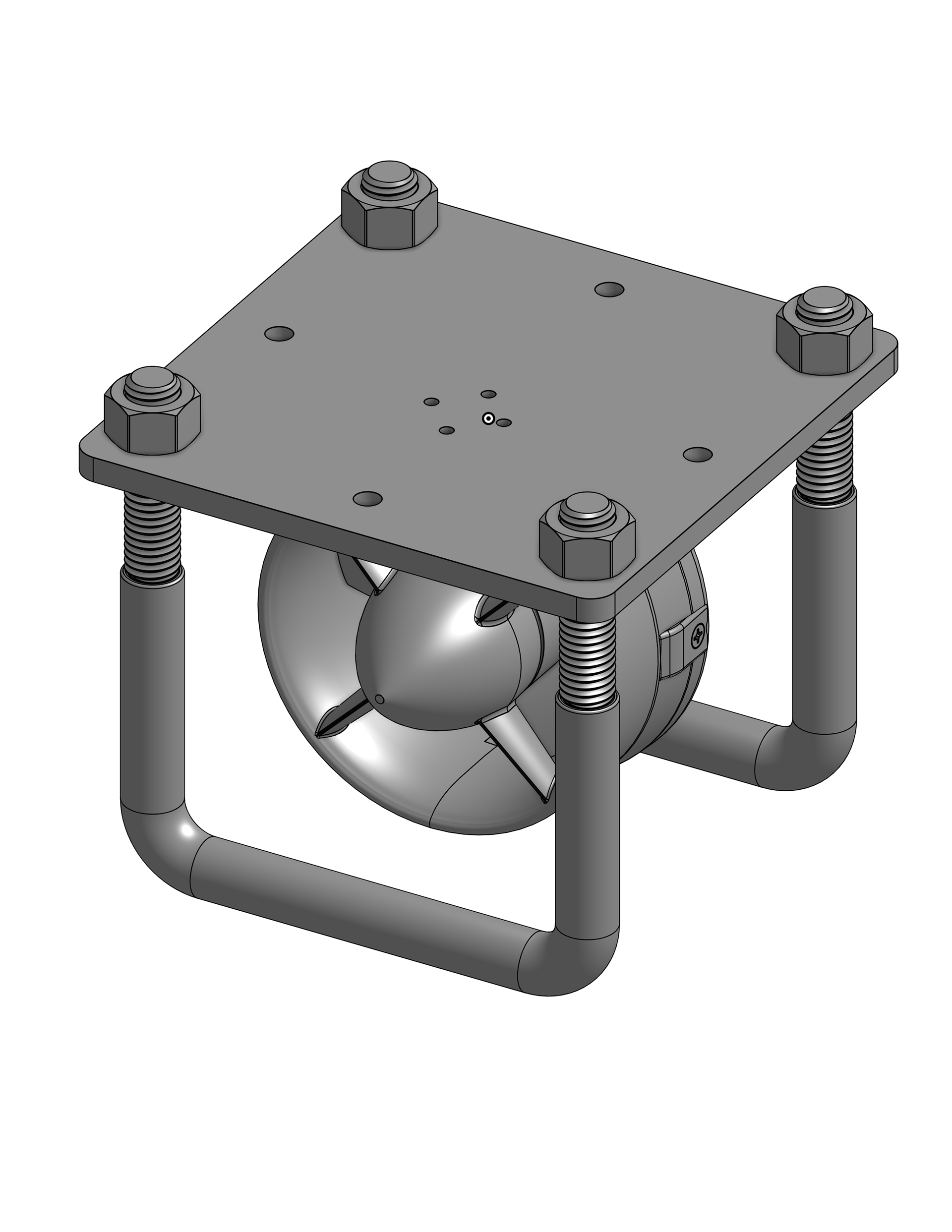
Thruster Shield CAD
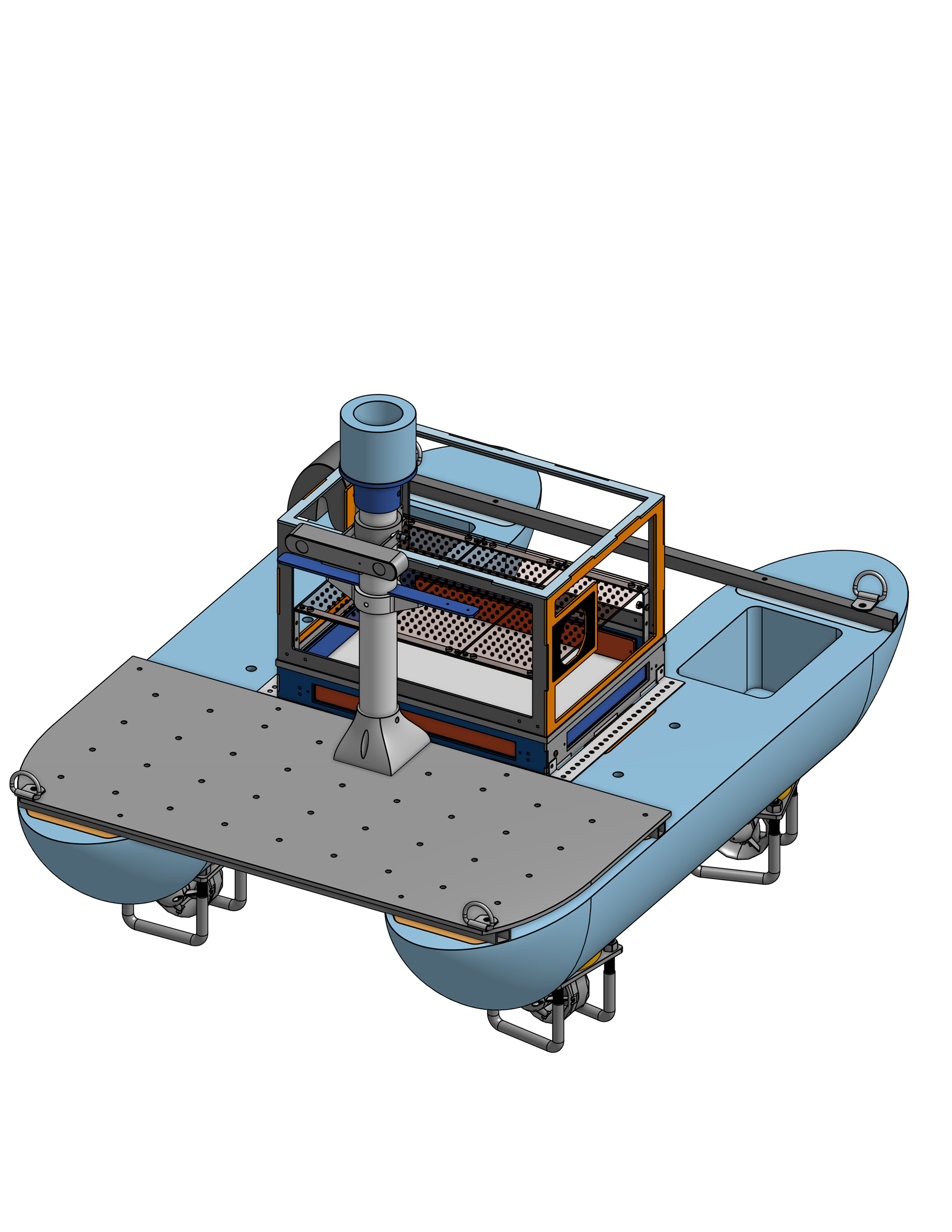
Fully assembled CAD
Performance Evaluation
After assembling the thruster onto the plate using T-Nuts and screws, we conducted load-bearing tests to assess its performance. The system was required to support the full weight of the boat on a single thruster without failure. The tests confirmed that the mounting system met the load requirements, proving both its structural integrity and functional adaptability.
Project Reflection
This project was a critical exercise in balancing the need for structural strength with the flexibility required by the boat’s X-Drive system. The success of the thruster mounting plate not only demonstrated the effectiveness of our design approach but also reinforced the importance of collaborative CAD work and precise fabrication methods. Future improvements could explore weight reduction strategies without compromising the system’s load-bearing capabilities.